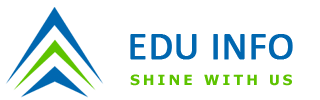
Vehicle Occupant Head Position Quantification Using an Array of Capacitive Proximity Sensors Currently, proper vehicle head restraint (HR) positioning requires manual adjustment and knowledge on the part of the occupant. By removing the requirement for manual adjustment, an HR positioning system that autonomously moves and adapts the HR position properly to any seated occupant could serve to reduce the social and personal costs of whiplash injuries, as compared with existing manual systems. To achieve this, quantification of the occupant’s head position relative to the HR is required. In a previous paper, a rectangular capacitive proximity-sensing array for the purpose of occupant head position quantification was studied. Here, a range-maximized sensor was first designed to reduce electrostatic and environmental disturbances. To achieve this, numerical modeling and laboratory experiments were conducted, and then, a design process for an interdigitated comb-shaped sensor geometry was proposed to maximize the sensing range of the sensor. The effects of temperature and humidity on the sensor were also evaluated and compensated. A novel capacitive proximity-sensing array was then designed, which had the minimum number of the aforementioned comb-shaped sensors necessary for accurately estimating the 3-D position of an occupant’s head in near real time. This estimation was carried out using a nonparametric neural network. The above capacitive array was then integrated and fully contained in a customized HR as part of a vehicle seat safety system. The system was tested and demonstrated that such a head position sensing methodology would be capable of autonomously positioning an HR to meet the guidelines of the Insurance Institute for Highway Safety (IIHS).